The following papers are to be presented within the framework of the session:
Uli Paschedag, Director Product Segment Underground - Caterpillar Global Mining
Plow Technology – History and Today‘s State-of-the-Art
ABSTRACT: Plowing is a long-known coal mining method invented in the early 1940s. Many different plow models were designed and trialed underground until in the mid-1990s only two models remained: the Reisshakenhobel® or base plate plow and the Gleithobel® or gliding plow. Horsepower and plow speed have increased steadily over time; however it wasn’t until 1989 when the biggest weakness of plow systems was overcome: automated plowing, using electrohydraulic controls, with defined cutting depths finally allowed plowing to become the most productive mining method for seams below 1.8 m seam thickness. This technology step like the most inventions in plowing came from Caterpillars predecessor Westfalia Lünen. Another milestone was yet another invention by Westfalia as the world’s first and only really mine-worthy and rugged control system PM 4 was introduced in 1993. Today, three standard plow systems are offered by Caterpillar together with tailor-made plow shields and the currently most advanced electronic shield control system, the PMC®-R. Installed cutting power of up to 2 x 800 kW, coupled with a blazing plow speed of up to 3.6 m/s and world-leading automation capabilities leads to an integrated longwall mining system for medium and thin seams which produces more clean coal at lower cost than any shearer can.
Zbigniew Stopa - Lubelski Węgiel Bogdanka S.A., Poland
Plough Technique at LW Bogdanka S.A. – Present State and Prospects of Development
Summary: The article discusses the experiences which the Bogdanka mine has gathered to date in the field of implementation of the plough technique. It presents technical specifications of the first mechanical plough system purchased by Lubelski Węgiel Bogdanka S.A. as well as the location, the geological and mining conditions, and the full production output reached by the research wall 1/VI in deposit 385/2 which was equipped with that system in 2010. The article discusses the second wall 7/VII/385, equipped with that system, launched at the end of September/beginning of October 2011 in the Stefanów field. It presents changes which were implemented in that system and in the technology of mining the second wall as well as the plans of the mine to purchase a second system, the delivery of which is forecast to take place in 2012.
Dr. David Xianguang Tang - China
Operational Experiences of Automated Plow Systems in Tiefa, China
ABSTRACT: There are eleven Cat (former Bucyrus/DBT) automated plow systems in China. Tiefa Coal Mining (Group) Co., Ltd. is not only the first end user but also has the largest fleet of the Cat automated plow system. Over the past decade it employed this fleet to effectively recover its valuable low seam reserves, which extended the service life of its old mines that otherwise could have been closed and resulted in the unemployment of thousands of miners. Meanwhile Tiefa gained a lot of successful experiences in using the automated plow systems and shared them with other Chinese coal producers.
This paper will describe how the problems were approached and successfully resolved by the Tiefa and will reflect China’s approach to effective resolution of thin seam coal extraction.
Andrzej Tor, DSc. Eng. - Jastrzębska Spółka Węglowa S.A., Jastrzębie-Zdrój, Poland
Past experience and further expectations with regard to application of plow technology at Jastrzębska Spółka Węglowa S.A.
ABSTRACT: The paper presents benefits that result from application of plow technology to extraction of thin seams as compared to conventional extraction with use of longwall shearers. The up-to-date experience and scope of further plans associated with coal extraction with use of plow systems at JSW plc are outlined with practical outcome acquired during past operations. Application of the plow technology with continuous improvements on the background of gained expertise and consequential innovative solutions are crucial for JSW plc due to substantial portion of thin seams in overall resources of comprised coal mines.
Michael Myszkowski - Caterpillar Global Mining, Luenen, Germany
Efficiency optimization of plow systems through the precise planning of new and comprehensive enhancement of operating longwalls
ABSTRACT: Plow technology reemerged and increased in importance in recent years, as many operators worldwide searched for an effective technology for extraction of thin and medium thickness coal seams. Plow systems were significantly improved in recent years. This resulted in higher production from plow faces. Nevertheless, there is an appreciable potential for further performance increase by the means of optimal technical, procedural and organizational improvements. Very important for the achieving of planned production rates is a correct design of plow faces. On the other hand, in many cases a performance improvement is possible without significant changes of the longwall system, simply requiring consistent analysis and effective realization of conclusions. The main message of this paper is: production can be strongly increased, even doubled, by paying careful attention to the correct design and optimal operation of a plow face.
Heinz-Werner Voss, RAG Anthrazit Ibbenbüren GmbH, Ibbenbüren, Germany, Holger Witthaus, RAG Mining Solutions GmbH, Herne, Germany
Plough longwall operations under challenging geological conditions
ABSTRACT: In German coal mining, comprehensive experience is available in the grading of geological faults. The available experience has produced a level of expertise which enables the maintenance of high production figures even under difficult conditions. This is demonstrated by the many successful projects of RAG. The paper describes in the following several successful case examples and illustrates that the collected know-how can be used globally, even for future challenges, by German RAG Mining Solutions GmbH to successfully operate modern high-performance plough companies under difficult conditions.
Stefan Bauckmann, Michael Myszkowski - Caterpillar Global Mining
Operational experiences with the plow system at the Pinnacle Mine in the USA"
ABSTRACT:This article provides a brief historical overview of longwall plow system deployment in the United States before describing the automated features and benefits of the highest-powered Bucyrus automated plow system that commenced service in November 2010 at the Pinnacle Mine near Pineville, West Virginia.
The plow was invented in Germany in 1941 and later refined by Wilhelm Löbbe, chief engineer at Westfalia Lünen (a predecessor company of Bucyrus Europe), in an attempt to modernize and mechanize underground coal mining. Löbbe also invented the ”Panzerförderer” or armored face conveyor (AFC) even prior to this date.
Löbbe improved plow performance by reducing the cutting depth and increasing the cutting speed. The ”fast plow”, having an installed power of approx. 2 x 140 hp (2 x 100 kW), achieved a daily output of over 1,100 sht (1,000 t )for the first time in 1950. By the mid 1980’s installed power had drastically increased to 2 x 340 hp (2 x 250 kW). To match this power the plow chain size increased also 34 mm diameter which allowed plow speeds of 350 ft/min (1.8 m/s) to be achieved.
Wladislav Kurtobashev - Russia
Contemporary plow technology in Russia
Jan Matula - OKD, a.s., Ostrava, Czech Republic
Experience with plow equipment at OKD
ABSTRACT: OKD has rich experience with plowing as the first mechanized shields were deployed already in 1973. New or completely refurbished plow sets with shields have been acquired in the scope of POP 2010 project between 2008 and 2011. OKD had high expectations when investing in new plow sets with a planned daily production exceeding 1,000 tons. However, these goals have not been achieved due to adverse geological conditions combined with equipment issues. It is expected that share of plow production will grow in future at OKD so the company needs to do its best to fix all the problems currently incurred at the operations.
R. J. Dyczkowski, J.W. Timoszenko – National mining university , Dnipropetrovsk, Ukraine
Technika strugowa w ukraińskich kopalniach węgla kamiennego
Dr. G. Philipp - THIELE GmbH & Co. KG, Iserlohn, Germany
Chains – boon or bane for modern plow technology?
ABSTRACT: The coal plow is an essential piece of equipment for winning under thin-seam conditions. Today’s plow installations, which deliver drive outputs of 2 x 800 kW, are equipped with chains 42 x 137 mm in size and can operate at speeds of up to 3.6 m/s. This places huge demands on the chains and their connecting links. Small face openings, which require low-height conveyor systems and coal plows with minimal guideway clearance, combined with the restricted amount of space available in the gate roads where the compact drive units have to operate, pose a real challenge for the geometry and quality of the plow chains. Achieving maximum face outputs regularly and without interruption, even when operating with highly-stressed plow chains, calls for real manufacturing and engineering skills on the part of the equipment suppliers and chain-makers combined with mining know-how and an effective preventive maintenance system on the part of the operator.
Marek Chagowski - Lubelski Węgiel Bogdanka S. A., Tadeusz Jędruś, Eng. Jan Lubryka, Dariusz Macierzyński - ELGÓR+ HANSEN Sp. z o. o.
Power supply, control and automation systems of the high-performance plough systems based on the example of LW Bogdanka S.A.
ABSTRACT: This paper presents the experience gained during development, implementation and commissioning of the high-performance plough system of new generation at LW Bogdanka SA and describes in detail the power and control system taking into account the automation process of plough systems.
Therefore it becomes necessary to develop power supply and control systems for the high performance plough systems, so as to offer on ongoing basis such electrical equipment, which will completely fulfil the technical and economic tasks. It should be emphasized that the plough technique poses numerous new challenges to be met by each element of the system - only overcoming these challenges guarantees full economic success for mining companies, that translates proportionally to the success of cooperating with them companies. The challenges set by the new generation of ploughing technique should result in development of other shearing machines, including shearer loaders not requiring direct handling. Certainly, particular importance will be assigned to non-contact switches enabling flexible adjustment of drive motor revolutions in mining machinery.
St. Prusek, S. Rajwa, A. Wrana, A. Walentek - Główny Instytut Górnictwa – Poland
Determination of cuttability of coal seams and the surrounding rocks in underground conditions by means of a device designed at GIG.
ABSTRACT: In this paper, a device for cuttability measurements of coal seams and the surrounding rocks in underground conditions, designed at GIG has been presented. Part of he article is dedicated for the review of cuttability measurement methods of rocks, applied in Poland and abroad so far. After that, the main elements of the device have been described as well as a procedure for performing measurements in underground conditions presented. Simultaneously, the examples of the underground measurement results have been given..
Zbigniew Gach, Michał Skrabaka, Tomasz Nosal, Rafał Holewa - Katowicki Holding Węglowy S.A. , Katowice, Poland
Mining of the hard coal seams in the mines belonging to the Katowicki Holding Węglowy using shearer longwall system
ABSTRACT: The possibilities for mining of the coal seams in mines belonging to the Katowicki Holding Węglowy are presented in this paper. Amount of coal which can be mined from coal seams was analyzed as well as its basic parameters i.e. heating value, ash content and sulphur content. Moreover technical specification of the shearer longwall system for low longwalls, manufactured by the Famur company, is presented. This system is used during mining of coal seams in KWK “Murcki-Staszic” Ruch “Staszic”.
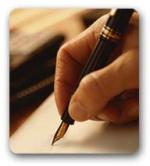